- HELP
- Technical Information
- CNC Turning
- Accuracy and Machining Specifications
- Dimensional tolerances that can be specified
Dimensional tolerances that can be specified
- When the 3D CAD data is uploaded, You can specify dimensional tolerances for areas where dimensions and tolerances are not displayed
- The minimum tolerance (range) that can be specified varies for each combination of geometry elements.
Fit Tolerance
The fit tolerances that can be set for lathe machining and secondary machining are as follows.
Type of Machining | Fit Tolerance |
---|---|
Lathe | Metal:Grade IT6 or above |
Resin:Grade IT7 or above | |
| Metal:Grade IT7 or above |
Resin:Grade IT7 or above |
Caution
- The following surface treatments cannot be specified with a tolerance range of less than 0.1.
- Surface Treatment|Trivalent Chromate (clear),Trivalent Chromate (black),Salt-Bath Nitrocarburizing,Hard Anodize (Clear)
Dimensional Tolerances for Full Length (L) and Length (ℓ)
The tolerances that can be set for the full length and the length of each element (part) are as follows.
[mm]
Metal | Full Length (L) and Length (ℓ) | |
---|---|---|
Example of Minimum Tolerance | Range | |
L,ℓ ≦ 200 * | ±0.02 | 0.04 |
200 < L, ℓ ≦ 500 | ±0.05 | 0.1 |
500 < L, ℓ | ±0.2 | 0.4 |
*The range that can be set will change for the following thin plates.
Metal | Full Length (L) and Length (ℓ) | ||
---|---|---|---|
Example of Minimum Tolerance | Range | ||
L ≦ 5 | 150<D | ±0.1 | 0.2 |
L<10 | 50 ≦ D |
Resin | Full Length (L) and Length (ℓ) | |
---|---|---|
Example of Minimum Tolerance | Range | |
L,ℓ ≦ 100 | ±0.05 | 0.1 |
100< L,ℓ ≦ 200 | ±0.1 | 0.2 |
200< L,ℓ ≦ 300 | ±0.2 | 0.4 |
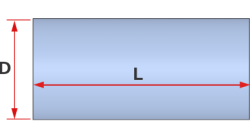
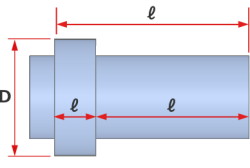
[mm]
Resin | Full Length (L) and Length (ℓ) | |
---|---|---|
Example of Minimum Tolerance | Range | |
L,ℓ ≦ 100 | ±0.05 | 0.1 |
100 < L, ℓ ≦ 200 | ±0.1 | 0.2 |
200 < L, ℓ ≦ 300 | ±0.2 | 0.4 |
Resin | Full Length (L) and Length (ℓ) | |
---|---|---|
Example of Minimum Tolerance | Range | |
L,ℓ ≦ 100 | ±0.05 | 0.1 |
100< L,ℓ ≦ 200 | ±0.1 | 0.2 |
200< L,ℓ ≦ 300 | ±0.2 | 0.4 |
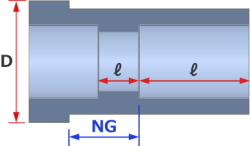
Tolerances for Groove Outer Diameter (D), Groove Width (w) and Location Dimensions (ℓ)
The tolerances that can be set for the outer diameter are as follows.
[mm]
Tolerances for Groove Outer Diameter (D) | Minimum Tolerance | Range |
---|---|---|
±0.02 | 0.04 |
Groove Width (w) | Minimum Tolerance | Range |
---|---|---|
±0.05 | 0.1 |
Position Dimensions (ℓ) | Minimum Tolerance | Range |
---|---|---|
ℓ≦150 | ±0.05 | 0.1 |
150<ℓ≦400 | ±0.15 | 0.3 |
400<ℓ | ±0.3 | 0.6 |
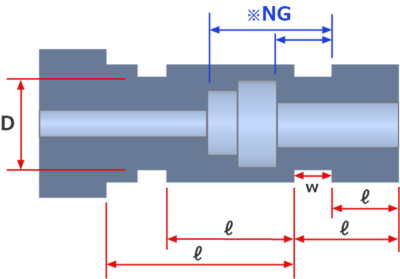
*Tolerance between inner and outer diameter surfaces cannot be added.
Tolerances for Groove Inner Diameter (d), Groove Width (w) and Location Dimensions (ℓ)
The tolerances that can be set for the inner diameter are as follows.
[mm]
Tolerances for Groove Inner Diameter (d) | Minimum Tolerance | Range |
---|---|---|
±0.05 | 0.1 |
Groove Width(w) | Minimum Tolerance | Range |
---|---|---|
±0.07 | 0.14 |
Location Dimensions(ℓ) | Minimum Tolerance | Range |
---|---|---|
±0.1 | 0.2 |
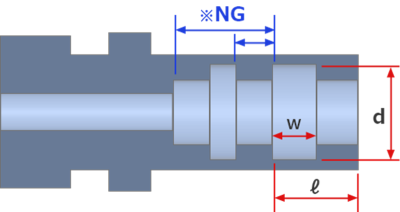
- *Tolerances cannot be added to the inner diameter groove and other elements.
- However, the positional dimension from the end face of the ℓ section is excluded.
Tolerances for Each Part
The tolerances that can be set between each shape element are as follows.
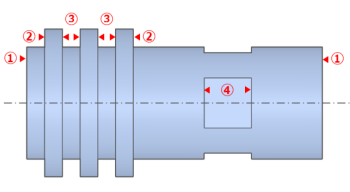
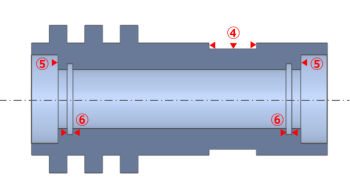
[mm]
No | Shape Element | (2) Outer Diameter Side/ (3) External Groove Side/ (4) Pocket Surface | (5) Inner Diameter Bottom | (6) Internal Groove Side |
---|---|---|---|---|
(1) | Both End Faces | 0.04~ | 0.04~ | 0.1~ |
(2) | Outer Diameter Side | |||
(3) | External Groove Side | – | – | |
(4) | Pocket Surface | |||
(5) | Inner Diameter Bottom | – | 0.04~ | |
(6) | Internal Groove Side | 0.04~ |
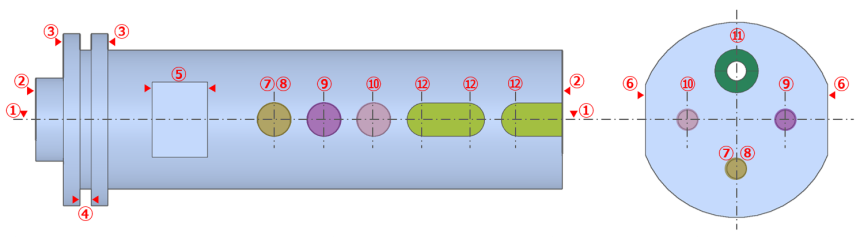
[mm]
No | Shape Element | (7) Precision Hole Center | (8) Straight Hole Center/ (9) Tapped Hole Center/ (10) Insert hole center/ (11) Countersink center | (12) Slotted Hole/Keyway |
---|---|---|---|---|
(1) | Center axis | 0.04~ | 0.2~ | – |
(2) | Both end faces | 0.04~ | ||
(3) | Outer Diameter Side | |||
(4) | External Groove Side | – | ||
(5) | Groove side face | 0.04~ | ||
(6) | External face | – | ||
(7) | Precision Hole Center | 0.2~ | 0.04~ | |
(8) | Straight Hole Center | 0.2~ | 0.2~ | |
(9) | Tapped Hole Center | |||
(10) | Insert hole center | |||
(11) | Countersink center | |||
(12) | Slotted Hole/Keyway | 0.04~ | 0.04~ |
Tip
- (1) Holes on the same circumference are called P.C.D. (Pitch Circle Diameter). Cross bores are not supported.
- (2) P.C.D is recognized even with different hole types.
- (3) P.C.D. is recognised regardless of whether the positions of the holes are equally or unequally divided.
- (4) It is possible to add diagonal dimensions that specify the distance between P.C.D. holes.
- How to use > Adding/Deleting Dimensions and Dimensional Tolerances
P.C.D. Equally divided | P.C.D. Unequally divided | The distance between P.C.D. holes. |
![]() |
![]() |
![]() |
Caution
- P.C.D. recognition is supplementary and reference information in meviy for CNC Turned parts.
- If you need to specify the tolerance between holes, please select the “Add tolerance” icon and specify the tolerance for the target position.
Tip
- The positional relationship of holes on both end faces of the reference model in the figure below is a general tolerance. Positional tolerances cannot be specified for topologically related shapes..
![]() |
![]() |
Notes
- 3D Model Colour Schemes
- If a colour scheme for an unsupported shape is displayed, automatic quotation is not available.
Geometric Tolerance
Surfaces and feature types available for geometric tolerance setting.
Configurable Surfaces
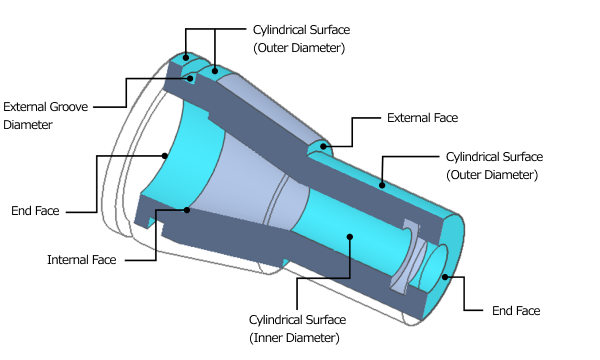
- Geometric tolerances cannot be specified for holes, keyways (both outer and inner diameters), notches (including pockets), inner diameter grooves, and end grooves.
- If a datum or geometric tolerance is specified on a threaded diameter, the tolerance is guaranteed based on the measured value before threading.
Configurable geometric tolerances
*Depending on the material and size, a manual quotation may need to be requested.
Geometric Tolerance Type | Symbol | Flat Face | Cylindrical Surface | Datum | Datum Reference Type | Tolerance value |
---|---|---|---|---|---|---|
Flatness | ![]() |
〇 | – | – | surface | 0.01~0.1 |
Parallelism | ![]() |
〇 | – | required | surface | 0.01~0.1 |
Perpendicularity | ![]() |
〇 | 〇 | required | surface | 0.01~0.1 |
Circularity | ![]() |
– | 〇 | – | surface | 0.01~0.1 |
Concentricity | ![]() |
– | 〇 | required | axis | 0.01~0.1 |
Straightness | ![]() |
– | 〇 | – | surface | 0.01~0.1 |
Cylindricity | ![]() |
– | 〇 | – | surface | 0.01~0.1 |
Circular Runout | ![]() |
– | 〇 | required | axis | 0.01~0.1 |
Total Runout | ![]() |
– | 〇 | required | axis | 0.01~0.1 |
Materials available for Geometric Tolerancing
Material | Geometric Tolerancing |
---|
Steel | 1045 Carbon Steel | 〇 |
---|---|---|
1018 Carbon Steel | 〇 | |
4135 Alloy Steel | 〇 | |
4140 Alloy Steel | 〇 | |
O1 Tool Steel | 〇 | |
D2 tool Steel | 〇 | |
H13 tool Steel | 〇 | |
52100 alloy Steel | 〇 | |
Stainless Steel | ー | 〇 |
304 SS | 〇 | |
316 SS | 〇 | |
440C SS | 〇 | |
Aluminum | ー | 〇 |
5056 | 〇 | |
6061 | 〇 | |
7075 | 〇 | |
Brass | ー | 〇 |
Resin | ー | ー |
Acetal(standard, white) | ー | |
MC Nylon(standard, blue) | ー | |
MC Nylon(weather resistance, black ash) | ー | |
ABS(standard, black) | ー | |
ABS(standard, natural color) | ー | |
PC(standard, transparent) | ー | |
PC(standard, black) | ー | |
PP(standard, natural color) | ー | |
PTFE(standard, white) | ー | |
PEEK(standard, gray-brown) | ー | |
PPS(standard, natural color) | ー | |
Acrylic(standard, transparent) | ー | |
UHMWPE(standard, white) | ー | |
PVC(standard, gray) | ー |
Surface Treatments available for Geometric Tolerancing
Surface Treatment | Geometric Tolerancing |
---|
Steel | Electroless Nickel Plating | 〇 |
---|---|---|
Hard Chrome plating | 〇 | |
Black Oxide | 〇 | |
Trivalent Chromate (clear) | × | |
Trivalent Chromate (black) | × | |
Salt-Bath Nitrocarburizing | 〇 | |
Low Temperature Black Chrome | × | |
Phosphate Coating | 〇 | |
Stainless Steel | ー | ー |
Aluminum | Clear Anodize | 〇 |
Black Anodize | 〇 | |
Black Anodize (matte) | 〇 | |
Hard Coat Anodize (Clear) | × | |
Brass | ー | ー |
Resin | ー | ー |
- *Resin conforms to [Geometric Tolerance Accuracy Standards for Lathe Machining] >>> Normal tolerance standard for machining dimensions without instructions
- *Hard chrome plating and salt-bath nitrocarburizing may require grinding after surface treatment depending on the required precision. The surface treatment will be removed by the grinding process.