- HELP
- Technical Information
- CNC Turning
- Design Guidelines
- Difference in Shapes Between the 3D Model and the Finished Product
Difference in Shapes Between the 3D Model and the Finished Product
- Points to Note for the Finished Shapes of Internal and External Corners of Lathe Parts
- Points to Note on Centering Holes
- Points to Note on the Bottom of Holes (Turning/Milling)
- Details for Internal Corners of Cylindrical Shapes
- Points to Note on Incomplete Threads
- Points to Note on the Tapered Thread (ISO)
- Points to Note on the Finished Shape of the End Face Groove Internal Corners
- Points to note regarding the finished shape of internal corners in pockets.
- Points to Note for slitting process
- Hexagonal Hole Information
Points to Note for the Finished Shapes of Internal and External Corners of Lathe Parts
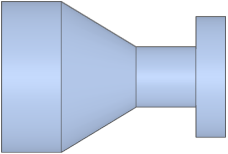

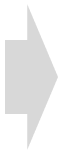
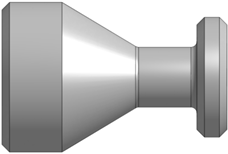
Tip
The finish conditions are as follows.
- Models with external corners of less than C/R0.5 will have C/R 0.1 to 0.4 mm or edge breaking.
- If the internal corners of the cylinder are less than 0.5 and there is no relief groove in the model, the tool edge will leave a corner of R0-R0.4mm.→Click here to specify “Corner R0” without modeling a relief groove.
Caution
- When modelled with C0.5 mm or more, machining will be in match the 3D data.
- When modelled with R0.5 mm or more, machining will be in match the 3D data.
Caution
Specification of “no chamfering” is not supported.Notes
-
- A standard retaining ring grooving tool has corner R0.2
- For retaining ring standards, click here.>>>Specifications for External Thread and Internal Thread, Keyways, Holes and Pockets
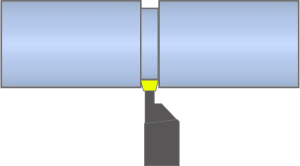
Outer diameter grooving
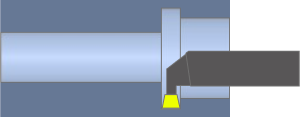
Inner diameter grooving
Points to Note on Centering Holes
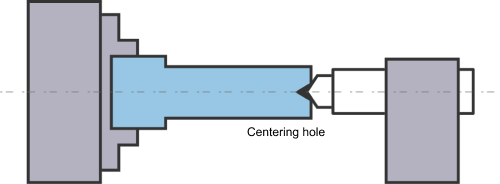
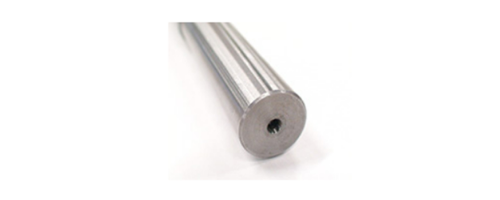
Caution
- “Centering hole cannot be left” can be selected, but there may be restrictions on the shapes that can be machined that make the option unavailable. When this occurs, check the “Important Information” in the upper-left corner of the screen.
Notes
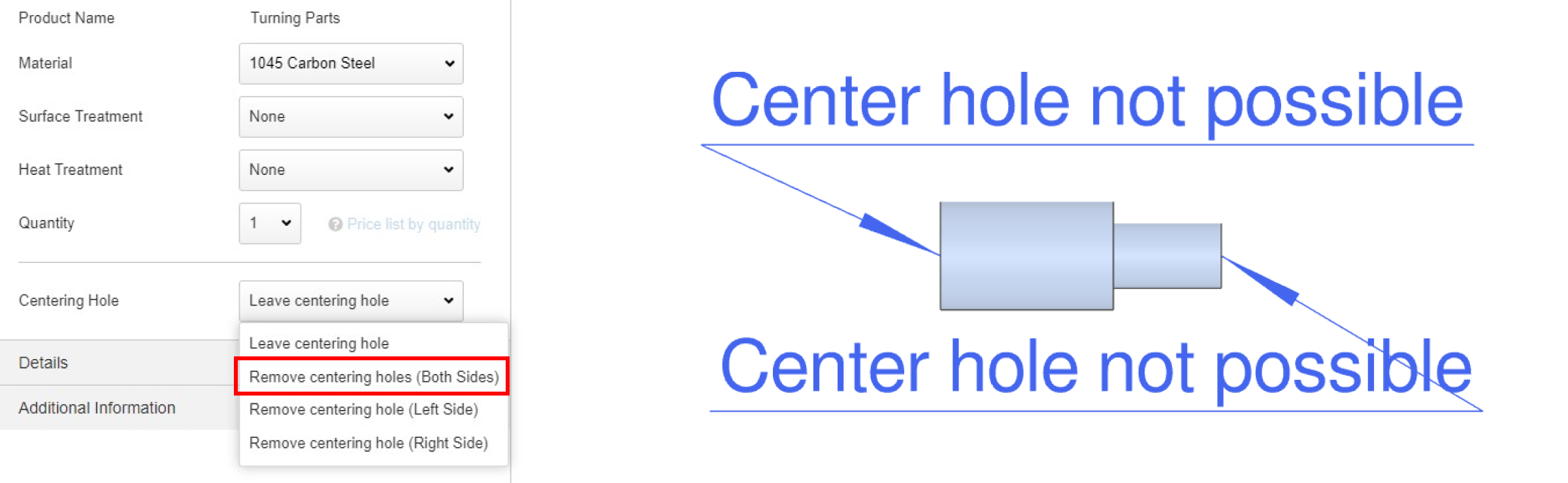
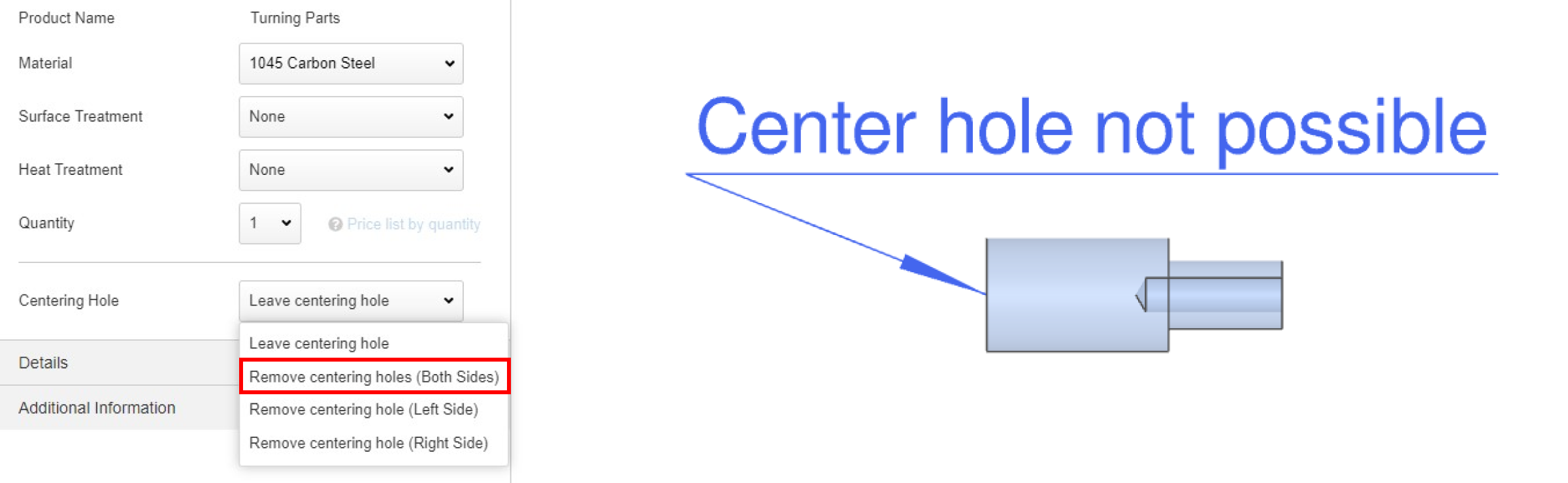
Points to Note on the Bottom of Holes (Turning/Milling)
Shape patterns | Inner diameter hole does not have a step | Inner diameter hole has a step |
---|---|---|
A | ![]() |
![]() |
Drill tip shape remains (flat bottom will be 1mm or more) | ||
B | ![]() |
![]() |
Drill tip shape remains, no flat bottom |
- The type of the bottom of the hole will depend on the diameter and depth of the hole.
- Example: If the inner diameter (D) is 10mm and the hole depth is 35mm, the depth of 35mm ÷ inner diameter of 10mm = 3.5D, so the bottom of the hole type will be B.
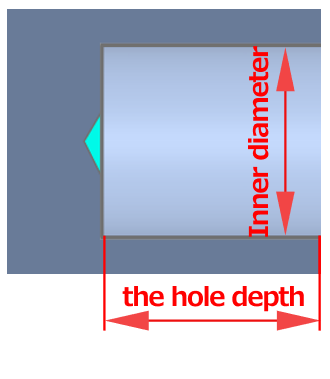
Inner diameter(D) | the hole depth | ||
---|---|---|---|
to 3D | 3D to 5D | 5D to 10D | |
D≦⌀6 | B | B | B |
⌀6 <D≦⌀30 | A | B | B |
⌀30<D | A | A | A |
If a flat bottom hole is required, please request it in “Additional Information”. We will confirm whether or not we can accommodate your request and reply.
Notes
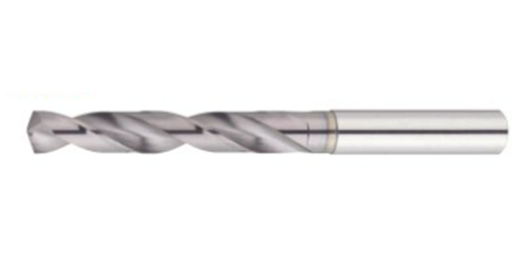
Details for Internal Corners of Cylindrical Shapes
Outer diameter
- When you want to minimize the corner R or specify a relief groove
- → Select “Corner R0”
- A relief groove will be machined to eliminate any radius left behind by the tool in the corner.
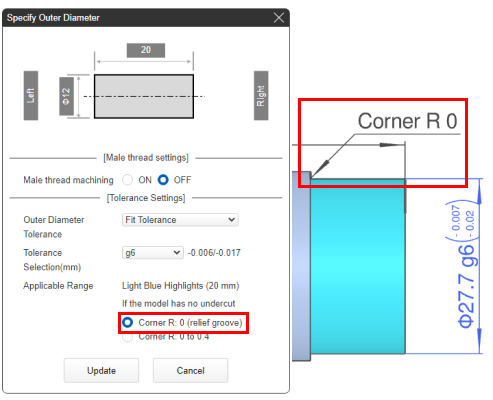
Tip
The width and depth of the relief added when selecting “Corner R0” can vary depending on the tools used. The exact dimensions cannot be specified.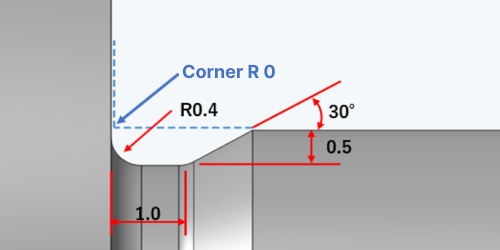
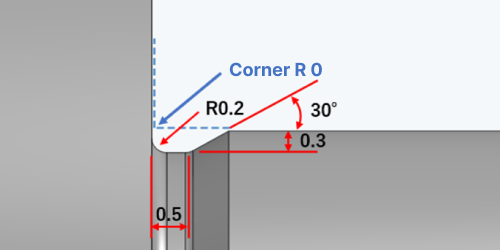
③ If the length of the shaft is short, it may be machined with a tool with a 0.1mm radius on the end that contacts the shaft.
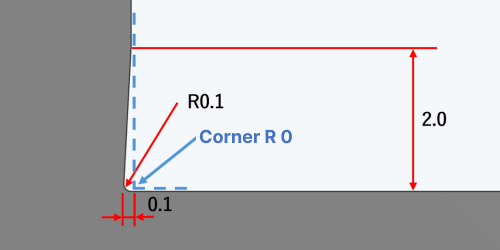
Notes
(1) The model has Corner R0.5 or greater | (2) The model has a relief groove |
![]() |
![]() |
- When the cylindrical corner can be any shape
- → Select “Corner R0 to R0.4”.
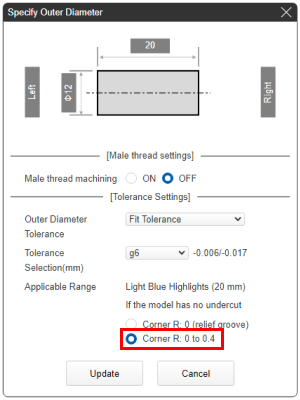
Tip
- Cylindrical corners with “Corner R0 to R0.4” can have the following shapes.
- ① Radius from machine tool remains.
- ② Relief groove is machined on the diameter only to achieve minimum clearance.
-
Machined diameter clearance groove.
Groove Dimensions
- ③ Relief groove is machined on the diameter and the face to achieve minimum clearance.
-
Machined diameter and face clearance grooves.
Groove Dimensions
Modeled radius exceeds R0.5
Machined diameter clearance groove.
Groove Dimensions
Inner diameter
Sharp Corner, R0
Undercut Groove
Undercut Groove with Lead
Notes
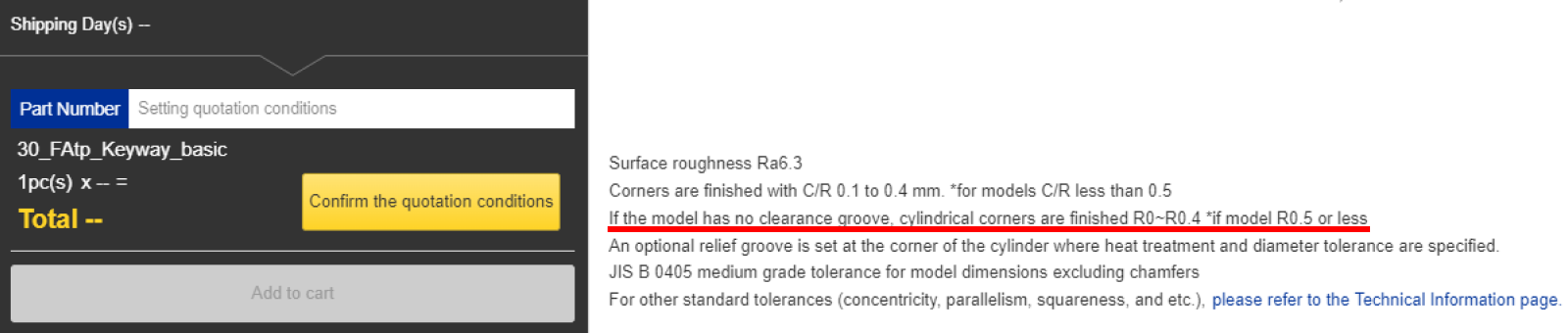
Points to Note on Incomplete Threads
- The required undercut shape (length and depth) to ensure the thread length with an incomplete threaded position is shown. See the example below.
- *If the model shape does not satisfy the following table (1) to (4), we will process it according to our recommended value.
[mm]
External Thread | Internal Thread | ||
---|---|---|---|
Modelling | Without undercut | ![]() |
![]() |
With undercut | ![]() |
![]() |
|
(1) Lower limit value of incomplete threaded portion length and undercut width | Pitch × 2.0 | Pitch × 2.5 + 2 | |
(2) Lower limit value of thread length (external thread) and thread depth (internal thread) | Pitch × 2.0 | Pitch × 2.0 | |
(3) Chamfered edge | Chamfered to prevent burrs | Chamfered to prevent burrs | |
(4) Minimum undercut depth value | Pitch × 0.75 | Pitch × 0.75 |
Caution
④Models for which “pitch × 0.75” or less is set for the (4) minimum undercut depth value can be machined, but machine marks will remain.Reference model
Actual finished shape after machining
Tip
- The [Notes] shown in the red box below describe the applicable thread length/thread depth.
Example 1) Outer diameter specification: male thread thread length 36.6mm = 44.6mm – 4.0(pitch) × 2.0 | Example 2) Inner diameter specification: female screw thread depth 11.0mm = 15.5mm – (1.0(pitch) × 2.5 + 2.0) |
![]() |
![]() |
Caution
- Modelled thread shape cannot be recognized. Specify the external thread and internal thread on the meviy screen.
Points to Note on the Tapered Thread (ISO)
- Although there are multiple methods for modeling tapered pipe threads, the diameter and depth of the tapered pilot hole will be machined in accordance with ISO standards (or JIS B 0203). The modeled shape and depth of the hole are for reference only.
- Other areas of the part that are not threaded, such as the area beyond the pilot hole, will be machined to the model.
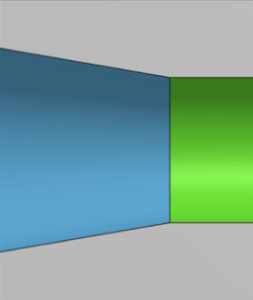
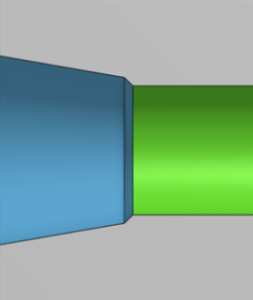
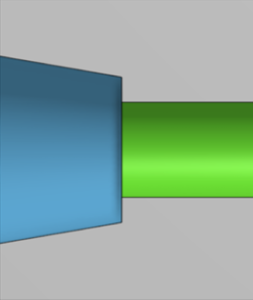
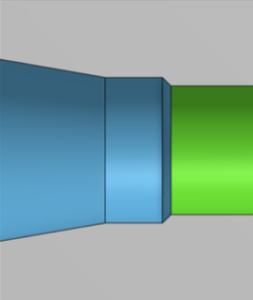
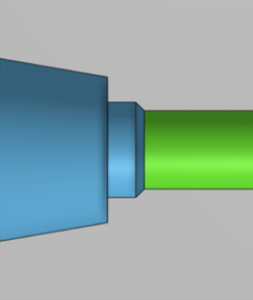
Machined according to ISO standards (or JIS B 0203)
Machined according to the model
Points to Note on the Finished Shape of the End Face Groove Internal Corners
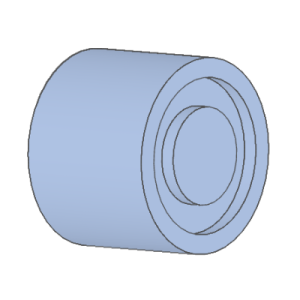
3D model with sharp edges in end face groove
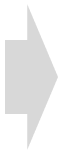
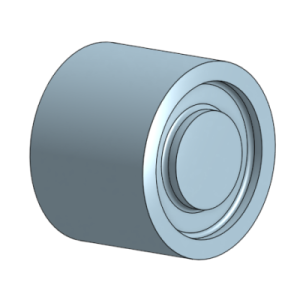
- Actual finished shape after machining
- *Finished with a radius (R) ranging from 0.1 to 0.5 mm.
Notes
No R modeling is required. The shape is finished with a radius (R) ranging from 0.1 to 0.5.Points to note regarding the finished shape of internal corners in pockets.
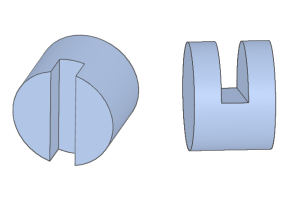
- Notch (pocket)
- Desined with a radius (R) less than 0.5 mm, including sharp edges.
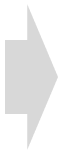
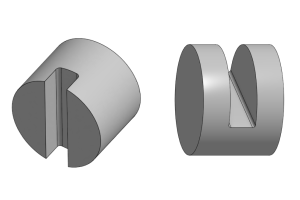
- Actual finished shape after machining
- *Finished with a radius (R) ranging from 0.1 to 0.5 mm.
Caution
- The curved shape on the sides of the pocket is determined by the tool diameter, but we choose tools with the smallest possible diameter.
- If there are any discrepancies between the model and the finished shape, we will contact you to discuss it after the order is placed.
Points to Note for slitting process
- The slitting process may change the dimensions of the part.
- The dimensions of the following shapes are guaranteed based on measurements taken prior to slitting.
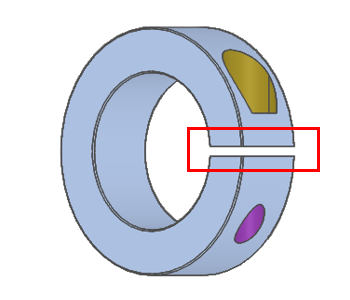
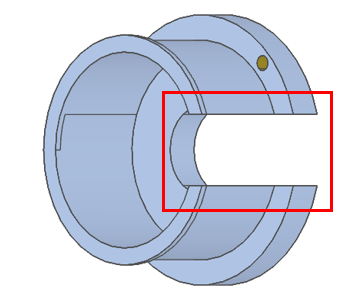
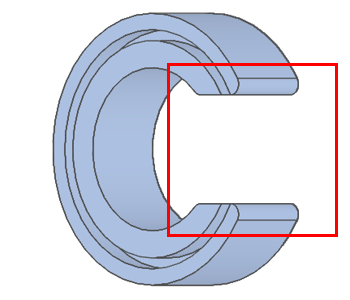
Hexagonal Hole Information
- The shape of the finished hexagonal hole will vary depending on the distance across the flats.
- The modeled depth is used as a reference, and the shape of the bottom of the hole will vary.
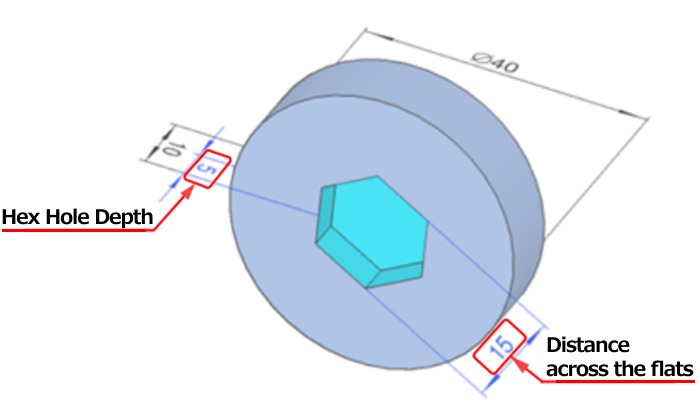
Distance across the flats | Metal | Resin |
---|---|---|
2 | Finished Shape① | |
2.5 | ||
3 | ||
4 | ||
5 | ||
6 | Finished Shape② | |
8 |
Caution
Specified surface roughness is not applied to the hexagonal hole.
Finished Shape①
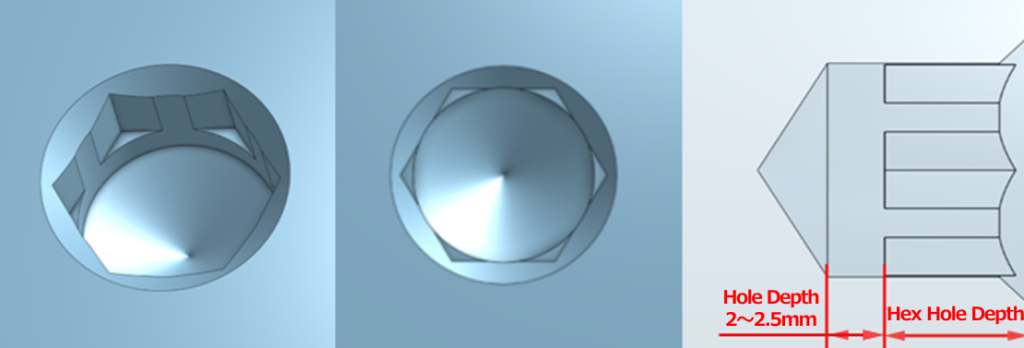
Distance across the flats | Metal | Resin |
---|---|---|
Other | Finished Shape② |
Notes
The tolerance for the distance across the flats conforms to JIS B 1176.
Finished Shape②
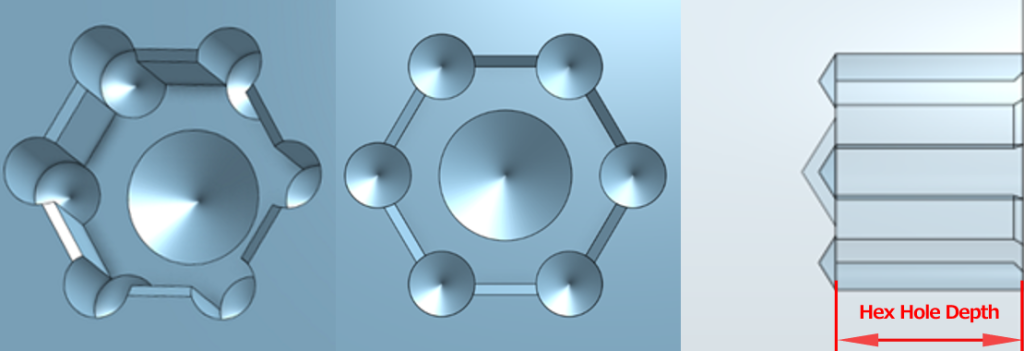